
Company:China Mineral Processing & Metallurgy League
Email: sales@hot-mining.com
Phone:+86 18252116933
Fax:+86 10 58646590
Address:Room10811, Floor8, Building A, Galaxy SOHO, Dongcheng Dist, Beijing, P.R.China
Did Jigging Technology Fade Away? An Ancient But NOT Outdated Process
Jigging is an ancient but mature coal washing technology by gravity. It has more than 110 years history since the application of air jigging machine. However, because the theoretical research of jigging coal washing technology is still wandering at the hypothesis stage, it also seriously relies on operator’s experience and skill, which results into no publicly recognized and uniform jigging intelligent operation standard in coal washing industry. What’s more, with the trend of improving coal product quality and coal washing efficiency, many coal washing plants chose to replace jigging by HMC(heavy medium cyclone). However, although the separation effect of heavy dense medium is better than jigging, the coal washing process is relatively complex with high cost. Therefore, it’s necessary to re-analyze whether there’s room for jigging process improvement.
Development and Application
Jigging is an ancient kind of mineral processing method by gravity. It was developed from original manual jigging to modern jigging machines with many different structural forms. It can be mainly divided into three types according to water turbulent method: ROM jig, piston jig and air-driven pulsating jig.
In year 1556, dolioform ROM Jigging Bath was used for mineral processing, since early 1800s it was applied into coal washing, and in 1950s, it spreaded all over coal mines in middle Europe.
In year 1820, German professor Dr. Hartz developed ROM Jig to fixed screen piston jig, and it was used for minrral processing by pulsating water flow, in 1840 it was used for coal washing. In year 1848, French professor Dr. Berard developed piston Jig for coal washing which can continuously work, it obtained British patent in year 1851, and was promoted to France, Belgium, Germany, USA and other countries. At the end of 1800s, German professor Dr. F. Baum invented hydraulic jig, the water was turbulent by using compressed air to slide the jig piston valve, which obtained patent on 26th September 1891. This kind of jig had good operability and was good for turbulent water to fit the feeding material characteristics.
The structure of Baum jig was simple in early stage, it consisted of U-type machine body, sliding piston valve and discharge manually. In 1930s, manually discharge was replaced by motor-driven or hydraulic pump-driven mechanical control. The sliding piston valve was changed to rotary piston valve in 1950s, and in 1960s it got a further development to electrically controlled pneumatic air valve, since 1980s, this kind of piston valve was controlled by computer numeric (CNC) gradually.
In year 1954, Japanese professors Dr. Gaosang and Dr Songcun proposed the air chamber jig under screen(TACUB jig) and it was applied at Chiping Coal Washing Plant in Hokkaido, in 1958. One feature of this jig is that, the air chamber was removed beneath fixed screen deck from side, it is lighter than Baum jig, and needs less space, also it is equally distributed along with the jig chamber water turbulence.
In major coal-producing countries, jigging coal washing method still plays dominant role. The development of screen side air chamber jig and underscreen air chamber jig is very fast. Since 1980s, many countries launches new type of jigging machine, many aspects have been improved a lot, like the geometric shape and configuration method of machine body, air chamber and piston valve structure, control system, air supply, water supply and feeding method and etc, traditional jigging machine moved forward to high efficiency, big capacity and full automation. At present each major coal producing countries are researching on technical weakness of jigging machine by using modern high technology. To solve the problem of 2/4~0.1mm fine particle coal low separation efficiency, complex vibration and trapezoidal wave jigging has completed industrial pilot test and achieved significant effect.
ROM Jig is original machine type of jigging technology, however it didn’t get popularization and application. Now new type product was developed and it can replace reject discarding by manual picking, maximum particle size could reach up to 300mm, with advantages of big capacity, good separation effect and less water consumption, which broadens application scope of jigging coal washing technology.
Separation Principle
Jigging coal washing technology means a kind of coal washing method by gravity, in the vertical fluctuating medium (mainly water), the feeding material realizes layering according to physico-mechanical properties(mainly density). Jigging coal washing technology is mainly divided into two processes, material layering and product separation.
Material Layering
1. When the pulsating waterflow rises, jig bed layer is lifted up and forms loose status. The mineral particles do relative movement each other according to their own features(density, particle size and shape) and starts layering.
2. When the waterflow stops rising and before it turns to be downward flow, due to inertia force, the mineral particles still moves and jig layer is still loose and stratificate.
3. When the waterflow drops, the jig layer is getting tight, but layering continues. When all mineral particles fall on the screen deck, they have lose possibility of relative movement each other, then the layering function stops.
4. When the waterflow stops droping, those ultrafine mineral particles go through gap of big materials and still move downwards, which extends lower limit of separation particle size, this phenomenon is called sip phenomenon, at last the jig layer gets completely tight and stops layering.
Product Separation
After many jigging cycles, the layering tends to perfection. Reject with high density concentrates at lower part of jig layer, while clean coal with low density concentrates at higher part. The jig bed moves forward along with horizontal flow, and finally the overflow is clean coal, material discharged on bottom is middlings and reject.
Principle Comparison Between Jig and HMC
HMC(heavy medium cyclone) separation technology totally depends on buoyancy generated by density of heavy suspension liquid. When the material is in medium, light density floats and heavy density sinks. However, for jigging processing, the layering status mainly depends on jigging intensity. If the jigging intensity is adjusted to be suitable and can keeps stable, the layering effect is good, otherwise will be not good. The separation density depends on requirement of product quality and set of jigging intensity and density separator.
Although the medium of jigging is water not heavy dense medium suspension liquid, it can adjust separation density to required degree like HMC(heavy medium cyclone). Thus we can see from comparison that, though the layering mechanism is different, separation principle is quite same, the layering effect shall be equal by rights. However, in actual production activities, the separation effect is worse than HMC(heavy medium cyclone), why?
For HMC(heavy medium cyclone), the control of medium density adjustment is stable, thus separation bed layer is steady, finally the separation effect is good and stable. If the separation density is changed frequently, the separation effect surely will be bad. On the contrary, for jigging coal washing technology, the jig machine need to adjust many kinds of parameters in real operation. If these parameters are not right and stable, the jigging intensity will changes and cannot keeps at one suitable intensity, then the separation accuracy is not good and effect is bad.
If you want to achieve good jigging coal washing effect, on one hand the pulsating waterflow shall keeps material on jigging screen deck with best vibration status, which will ensure best material loose degree, it will benefit material density layering; on the other hand, the discharging shall be punctual and timely, thus the layer will have a steady thickness and the product quality can be ensured, meanwhile less clean coal loss. Therefore, adjust jigging intensity to be stable and accurate from these two aspects, pay more attention on intelligent operation management, eliminate anthropogenic impact, then the separation effect of jigging machine will be improved greatly, even can be better than HMC(heavy medium cyclone) coal washing effect.
Typical Jigging Process System
Advantages of Jigging Process
MOST IMPORTANTLY, THESE ADVANTAGES ARE NOT FOR HARD-WASHED COAL.
-
Simple process flow and low CAPEX
-
Low OPEX: easy maintenance and management
-
More suitable for easy-slimed ROM than HMC(heavy medium cyclone)
MES Jigging Product Series
SHOWCASE
3D AND MODULE-DESIGNED JIGGING COAL WASHING PLANT
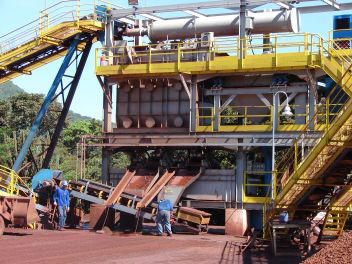
MMX CORUMBA COAL WASHING PLANT AT BORDER OF BRAZIL AND BOLIVIA
PARTIAL - 3D DESIGN JIGGING COAL WASHING PLANT
PARTIAL - 3D DESIGN JIGGING COAL WASHING PLANT
PARTIAL - 3D DESIGN JIGGING COAL WASHING PLANT
PARTIAL - 3D DESIGN JIGGING COAL WASHING PLANT
OVERALL DESIGN OF JIGGING PLANT BY MES
As an experienced international engineering company, HOT Mining has delivered dozens of JIG and HMC coal washing plant in China and overseas, from design stage(feasibility study, preliminary design and construction design), crucial equipment supply(Jig, Spiral,TBS, Cyclone, Centrifuge, flotation cell and flotation column) to operation management and system upgrade.
More info, please contact us at:
|
Serena Fu | Teresa Zheng |
E-mail |
serena.fu@hot-mining.com | teresa.zheng@hot-mining.com |
Whatsapp |
+86 15108333341 | +86 15281626323 |
Or visit web: www.hotminingepc.com/www.miningmes.com