
Company:China Mineral Processing & Metallurgy League
Email: sales@hot-mining.com
Phone:+86 18252116933
Fax:+86 10 58646590
Address:Room10811, Floor8, Building A, Galaxy SOHO, Dongcheng Dist, Beijing, P.R.China
The Factors Affecting the Moisture of Coal from Coarse Coal Centrifuge
Application of coarse coal centrifuge
Problems with coarse coal centrifuges
The coal slurry is graded by cyclone, then it is further dehydrated and graded by sieve bend screen, and finally dehydrated in coarse coal centrifuge. From the technical characteristics of the coarse coal centrifuge and the requirements of the operating instructions, the system meets the technical requirements of the coarse coal centrifuge, the generated materials basically meet the equipment to adapt to the feeding conditions (feeding concentration of 50% ~ 60%), so that it should be able to obtain the ideal product moisture. But, in the commissioning, the water content of the product from centrifuge is up to more than 30%, a long-term adjustment cannot solve this problem. To that end, HOT Mining's engineers visited a coal preparation plant in Huainan, China, that had earlier used coarse coal centrifuges. When Huainan coal preparation plant was put into operation, the recovery system of coarse coal slime was not normal, and the product moisture was very high. After many years of transformation, the product can achieve satisfactory moisture index. From this point of view, the plants which operated coarse coal centrifuge for the first time encountered the same trouble, is the product moisture is high.
Factors of higher moisture in coarse coal centrifuge products
It is found from the production transformation of Huainan coal preparation plant for many years that the product moisture of the coarse coal centrifuge is closely related to the particle size composition of the feed. Under the condition of constant feed concentration, when the fine slime content of <80 mesh in the feed is about 10% (maximum cannot exceed 15%), the product moisture can be controlled at about 12%. With the content of < 80 mesh fine slime increased, the product moisture increased greatly. Therefore, controlling the fine slime content of <80 mesh in the feed is the key to controlling the moisture of the product. In view of the above problems, we carried out a screening test on the coarse coal slime in the Inner Mongolia coal preparation plant, and the test results are shown in table 1.
It can be seen from Table 1 that the content of fine slime of <80 mesh up screen is as high as 31167%. Based on the production experience of Huainan coal preparation plant, it can be concluded that the high content of fine slime cause high product moisture.
The method reduces the moisture of the product from coarse coal centrifuge
The main reason for the high content of < 80 mesh fine slime is bad grading effect obviously. The solution to this problem is to improve the efficiency of classification equipment. Based on the production experience of Xinjiyi coal preparation plant, we adjusted the coarse coal slime classification system as following:
Changed the production system from intermittent production to continuous production, which ensured the feeding stability of cyclone and improved the classification efficiency of cyclone.
Changed the screen mesh of sieve bend screen from 0.135mm to 0.15mm, which improved the secondary grading effect. Thus, the overall grading efficiency of the grading system was improved.
The result of the transformation was that the moisture of the coarse coal centrifuge fell down and basically reached the expected water content. The product is loose.
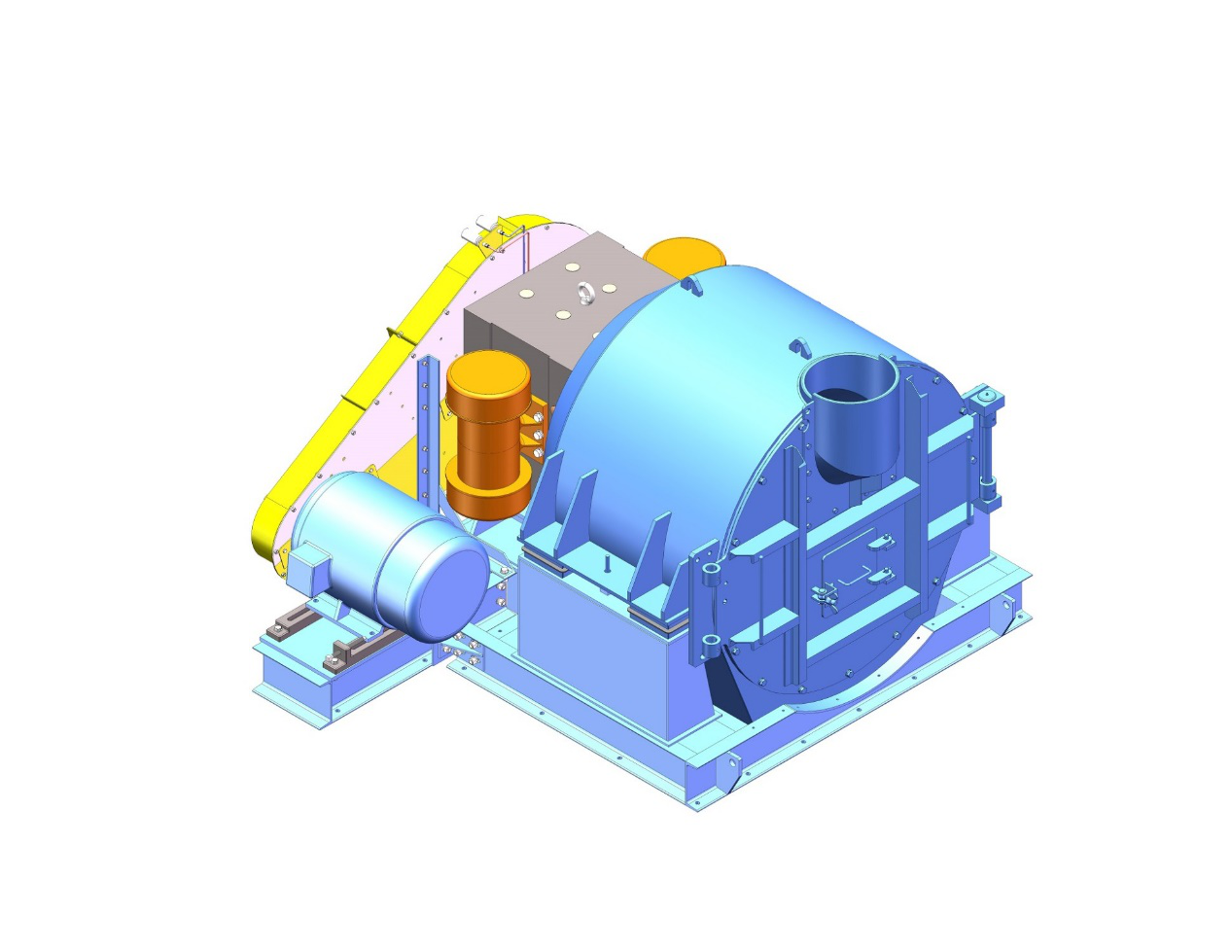
Conclusion
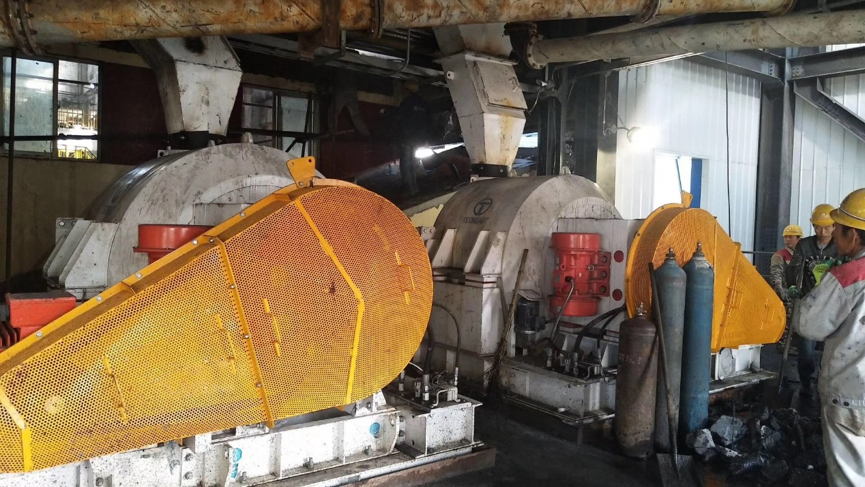
Any more information about coal washing plant or centrifuge, can contact us:
Kira Zhang, International Business Manager
Email: kira.zhang@hot-mining.com
Tel/WA:+86 15281051932
Teresa Zheng, International Business Manager
Email: teresa.zheng@hot-mining.com
Tel/WA:+86 15281626323
Tari Wang, Mineral Process Engineer & Centrifuge Products Manager
Email: tari.wang@hot-mining.com
Tel/WA:+86 15927349651