The Most Practical Technology in Coal Preparation Plant
Ten common faults of screening machine and their solutions
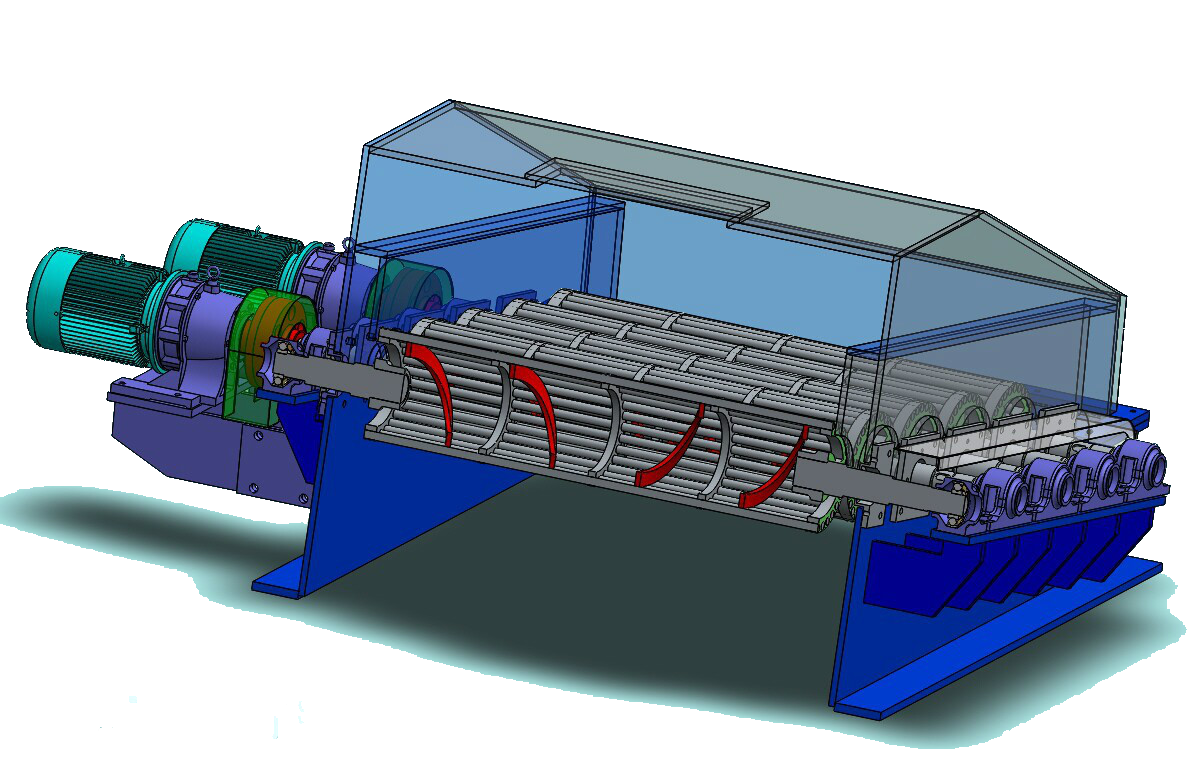
Fault 1: screen does not vibrate
Phenomenon: the motor only hums and does not start
Treatment: check the motor, check the vibration exciter, and deal with it.
Fault 2: exciter overheating
Phenomenon: the temperature of exciter exceeds the specified temperature
Treatment: check the oil, oil quality and oil quantity, check the bearings and gears, and replace the exciter if there is any problem.
Fault 3: high vibration
Phenomenon: the sound is loud in steel structure support
Treatment: check whether the fixed steel parts interfere with the screen body, whether there is material accumulation on the chute, whether the spring is damaged, and deal with it accordingly.
Fault 4: abnormal sound
Phenomenon: abnormal sound during operation
Treatment: stop the machine and check whether the spring is damaged, whether there are loose parts, whether the exciter cover is damaged, whether the bearing is damaged, whether the exciter gear is damaged, and make corresponding treatment.
Fault 5: too much material under screen
Phenomenon: too much material under screen
Treatment: check the screen plate for wear or breakage, and replace it.
Fault 6: the material on the screen is smaller than the material through the screen
Phenomenon: the material on the screen is smaller than the material through the screen
Treatment: insufficient water spray or clogged sieve plate hole, increase water spray volume or increase the number of spray nozzles or adjust the spray angle, clean or replace sieve plate.
Fault 7: uneven incoming materials
Phenomenon: the thickness of left, middle and right of screen material is not equal
Treatment: the foreign matters in the feeding part are blocked, and stop for cleaning.
Fault 8: rubber connecting plate damaged
Phenomenon: the rubber disk has cracks or noise here
Treatment: check whether the connecting shaft is in a straight line, readjust and replace the connecting disk.
Fault 9: rail seat beam broken
Phenomenon: abnormal sound under screen surface
Treatment: check the rail seat beam. If the broken rail seat beam does not contact the girder, repair welding can be conducted in case of emergency treatment; replace the rail seat beam.
Fault 10: irregular motion of screen machine
Phenomenon: abnormal screen vibration
Treatment: check whether the spring is damaged, whether the screen plate is loose, whether the screen surface is blocked by material accumulation, whether the material flows to one side of the screen machine, whether the beam screen side is broken, and make corresponding treatment.
Five common faults of crusher and their solutions
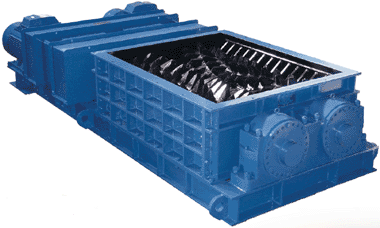
Fault 1: Super granularity
Phenomenon: lots of coarse coal
Treatment: check whether the crusher tooth plate is broken, whether the tooth of the tooth plate is broken, whether the tooth plate is worn, and replace the tooth plate.
Fault 2: can not be broken
Phenomenon: the motor rotates, the reducer rotates, and the coal overflows from the crusher
Solution: cut off the power and check the coupling from reducer to crusher.
Fault 3: shutdown in operation
Phenomenon: locked rotor alarm
Treatment: check whether there is hard blockage in the crusher after power failure, and check whether the locked rotor switch is normal, and deal with it.
Fault 4: main bearing temperature too high
Phenomenon: the temperature of main bearing exceeds the specified temperature
Treatment: check the amount of grease and pollution, check whether the bearing is damaged and deal with it.
Fault 5: reduced processing power
Phenomenon: the motor rotates, the reducer rotates, and a small amount of coal overflows from the crusher
Treatment: check whether the hydraulic coupling leaks is damaged, and then handle it.
Four common faults of coal feeder and their solutions
Fault 1: feeder does not discharge
Treatment: check the running direction of the two motors and whether the soft connection is broken.
Fault 2: uneven cutting
Treatment: check whether there is coal deposit on the bottom plate.
Fault 3: motor overload
Treatment: check whether there is much coal around the bottom plate and dustpan, resulting in no gap between the dustpan and the discharge chute.
Fault 4: backward coal overflow
Treatment: due to the small slope of dustpan, large moisture content of coal or large feeding amount, adjust the slope and feeding ram.
Nine common faults of belt conveyor and their solutions
Fault 1: the reducer does not rotate
Phenomenon: the belt motor and hydraulic coupling are running, the reducer is not running, the hydraulic coupling fusible plug is normal, the oil level is normal, the backstop is free of temperature and peculiar smell.
Treatment: from easy to difficult troubleshooting, first check the reducer, then check and replace the backstop, and then check the hydraulic coupling.
Fault 2: the belt conveyor fails to start
Phenomenon: the motor does not run.
Treatment: check and remove the protection faults (stall alarm, dredge the chute, reset the pull rope switch, reset the emergency stop button), and check the motor.
Fault 3: belt deviation
Phenomenon: when the belt conveyor is in normal operation, the belt starts to deviate along a certain point.
Treatment: check whether there is slime or sundries on the roller and idler, check whether there is too much coal on the lower belt, and clean it.
Phenomenon: the whole conveyor belt runs to one side.
Treatment: drum is not parallel, mostly due to tail drum deflection or tail drum slime.
Phenomenon: the belt runs to one side, and the deviation is at the joint of the belt.
Treatment: if the joint is not correct, it shall be remade according to the standard.
Phenomenon: the direction of belt deviation is uncertain, left and right.
Treatment: insufficient tension, adjust the belt tension.
Phenomenon: the belt does not deviate under no load, and it deviates under load.
Treatment: adjust the coal dropping point or increase the supporting roller if the material falling is partial or the supporting roller under the loading point is damaged or missing.
Phenomenon: the middle part of the belt conveyor deviates.
Treatment: move the deviation idler according to the situation.
Fault 4: belt damage
Phenomenon: the belt stops running and is damaged
Treatment: the belt is seriously deviated, and the belt joint is torn on the frame or roller bearing seat; check whether the equipment parts fall off, the iron is stuck in the blanking chute and the belt room; whether there is large coal and gangue; whether there is chute liner fall off; the transmission roller stalls; the roller and the idler are damaged and scratched; the idler is stuck and inflexible; there is iron wire and other sundries stuck between the cleaner and the belt 。
Fault 5: tape slipping
Phenomenon: the resistance of the tape is too large.
Treatment: loading goods should not be too much and there should not be a large number of idlers that do not rotate.
Phenomenon: the tape tension is small.
Treatment: adjust the tension device, adjust the deformation and elongation of the new belt after a period of operation.
Phenomenon: the friction coefficient between the belt and the driving drum decreases.
Treatment: avoid the contact surface of the belt driving roller from entering mud water or washing water when cleaning.
Fault 6: Spray
Phenomenon: spray material at transfer point.
Treatment: spray materials in chute and guide chute, check whether the conveyor is seriously overloaded and whether the rubber apron of guide chute is damaged.
Phenomenon: sprinkling in case of deviation.
Treatment: adjust the deviation of the tape.
Phenomenon: when the conveyor is started, the concave section will spring up and sprinkle materials.
Treatment: the concave part of the conveyor is provided with a belt pulley to prevent the belt from springing up.
Fault 7: abnormal noise
Phenomenon: noise caused by serious eccentricity of idler.
Treatment: replace the idler.
Phenomenon: noise when two shafts of coupling are not concentric.
Treatment: adjust the position of motor and reducer.
Phenomenon: abnormal noise of steering drum and driving drum
Treatment: check the bearing at the bearing seat.
Fault 8: short belt life
Phenomenon: the service life of conveyor belt is short.
Treatment: check whether the tape has been stored for a long time and cracks. Check the tightness of the cleaner to ensure that there is no material on the return tape.
Fault 9: broken belt
Phenomenon: the belt breaks during operation.
Treatment: check whether the belt is overloaded, pull the empty belt when the machine is stopped, avoid heavy load starting, replace the idler without rotation in time, clean up the sundries and reduce the running resistance of the belt.
Phenomenon: fracture from joint.
Treatment: if the tensile strength of the belt joint is not enough, the belt joint shall be checked frequently and replaced regularly, and the damaged joint shall be replaced in time.
Five common faults of scraper and their solutions
Fault 1: chain jumping
Phenomenon: scraper chain jumps at sprocket
Treatment: the installation position of the connecting ring or the ring chain is readjusted due to incorrect installation of the connecting ring or "twist" of the ring chain; the sprocket teeth are excessively worn, and the new sprocket is replaced; the scraper chain is too loose, and it is re connected.
Fault 2: shutdown
Phenomenon: trip
Treatment: due to over-current and heavy load, check and take out stuck materials.
Fault 3: bent scraper
Phenomenon: the blanking is not correct, the hard object is stuck in the sprocket, and the scraper is bent
Solution: cut off the power, loosen the tail roller and take out the hard object, adjust the chain and replace the scraper.
Fault 4: broken chain
Phenomenon: Operation interruption chain
Treatment: due to impact and fatigue fracture, serious wear or corrosion, poor chain manufacturing quality, the corresponding measures are to reduce the dynamic load, replace the severely worn and corroded chain, and replace the unqualified chain.
Fault 5: floating chain
Phenomenon: chain goes up and down, left and right in operation
Treatment: the possible reason is that the groove bottom is uneven or small particles enter under the chain. The corresponding solution is to correct the groove bottom and add a cleaning plate.
21 kinds of common faults of filter press and their solutions
Fault 1: insufficient pressure
Treatment: the overflow valve is damaged, repaired or replaced; the oil level is not enough, supplement the hydraulic oil; the oil pump is damaged, replace the oil pump ; the valve block and the joint are leaking, tighten or replace the O-ring; the oil cylinder sealing ring is worn, replace the sealing ring.
Fault 2: poor pressure maintaining
Treatment: the piston sealing ring is worn, replace the sealing ring; the oil way leaks, repair the oil way; the hydraulic control check valve is blocked or worn, clean or replace; the electromagnetic ball valve is blocked or worn, clean or replace.
Fault 3: broken filter plate
Treatment: If the feed pressure is too high during filtration, adjust the feed pressure; if the feed temperature is too high, change the high temperature plate or cool it before filtration; if the feed speed is too fast, reduce the feed speed; if the feed hole of the filter plate is blocked, clean the feed hole; if the filter cloth is damaged and the outlet is blocked, replace the filter cloth and clean it; if the coal cake is not full, clean and check to make the coal cake full.
Fault 4: filter plate up
Treatment: the installation foundation is not flat, and the foundation shall be reconditioned; the slag at the lower part of the filter plate is not clean, and it shall be cleaned.
Fault 5: the filtrate is not clear
Treatment: if the filter cloth is damaged, replace the filter cloth; if the filter cloth is not properly selected, retest and replace the filter cloth; if the opening of the filter cloth is too large, replace the filter cloth; if the suture of the filter cloth is opened, re suture.
Fault 6: noise in hydraulic system
Treatment: inhale air, open vent valve to vent; The fasteners are loose,tighten; excessive viscosity of hydraulic oil, reducing viscosity of hydraulic oil.
Fault 7: bent girder
Treatment: if the roughness of the foundation at the oil cylinder end is not enough, reinstall it; if the arrangement of the filter plates is not parallel and the pulling plates are not synchronous, rearrange the filter plates and adjust the synchronicity of the pulling plate trolley; if the head plates are not correct, the filter press support frame is deformed, and adjust it.
Fault 8: trolley does not pull the plate
Treatment: if the limit switch has no signal, adjust the position of the head plate; if the trolley is not in place, adjust the position of the trolley; if Y4 and Y5 do not act, replace Y4 and Y5 relays.
Fault 9: the filter cloth is damaged
Treatment: wash the filter cloth in time if there is much slime on it; replace the underflow nozzle if the primary cyclone runs rough.
Fault 10: Plywood timeout alarm
Treatment: if the closing proximity switch is broken, replace the proximity switch; if the pulling motor and frequency converter or reducer and chain drive mechanism are in fault, check and repair.
Fault 11: pressing timeout alarm
Treatment: the electric contact pressure gauge is damaged, check and replace; the hydraulic system is in fault, check and repair.
Fault 12: feed valve timeout alarm
Treatment: if the solenoid valve does not act, check and replace it; if the travel switch is broken, check and repair it; if the air pressure is not enough, check and repair it.
Fault 13: feeding pump fails to load normally after starting
Treatment: the coupling of motor and pump is damaged, check and repair; the feed pipe is blocked, clean.
Fault 14: shotcreting
Treatment method: the pressing force is not enough, increase the pressing force; the edge of the filter plate is mixed with slime, clean the slime; the filter cloth is folded, and the filter cloth is leveled.
Fault 15: stop pin does not move up and down
Treatment: if the proximity switch is in poor contact, check and replace the proximity switch; if the retaining pin mechanism fails, check the brake motor.
Fault 16: intake valve cannot be opened during pressing
Treatment: check the air compressor for low air inlet pressure; replace the air inlet pressure gauge if it is broken.
Fault 17: the filtrate pipe of the pressing time-space plate runs out of air
Treatment: if the filter plate is damaged, check and replace the filter plate; if the sealing ring of the air inlet of the filter plate is off, make up the sealing ring.
Fault 18: unloading release, panel shows release timeout
Treatment: The release proximity switch is broken, replace it; Hydraulic failure, check and repair.
Fault 19: head plate displacement too slow
Treatment: the oil on the high-pressure and low-pressure oil pumps is not normal, repair the oil filter, discharge the air in the pump, and check the performance of the high-pressure and low-pressure oil pumps.
Fault 20: the plate pulling device frequently impacts the handle of the filter plate, but does not return
Treatment: the oil for pulling plate is insufficient, the pressure relay does not act, adjust the flow of pressure relay spring and speed regulating valve, and increase the oil circuit pressure.
Fault 21: the oil pump is hot and does not supply oil
Treatment: if the motor or oil pump is not turned correctly, the oil is dirty, the oil level is low, the oil pump has problems, etc., adjust the rotation direction of the oil pump or motor; clean the oil pump and oil filter; refuel, check the oil pump, etc.
Nine common faults of magnetic separator and their solutions
Fault 1: magnetic separation efficiency decreases
Treatment: check whether the water level is low, reduce the discharge diameter of the tail until a certain amount of overflow overflows the downflow weir; The position of the magnet may be incorrect. If the concentrate is thick, rotate the magnet toward the discharge end.
If the concentrate is thin, rotate the magnet toward the feeding end; if the running gap is too large, readjust the roller position to reach the correct gap size; if the feeding coal slime is mixed with soil, use flocculant to remove the soil in the thickener;
If the screen gap of the demineralization screen becomes large or there is damage, the large particles entering the separation tank will increase and not be cleaned in time, resulting in no overflow or less overflow, which will shorten the magnetic separation area. The screen plate shall be replaced, and the materials in the separation tank must be flushed before starting each shift; the feed slime is mixed with flocculant, and the flocculant shall be removed from the thickener by using dispersant;
Fault 2: too much overflow
Treatment method: if the discharge diameter is too small, increase the discharge at the tail of the machine until a certain amount of overflow overflows the downflow weir; if the solid content of the feed is too high, increase the operation gap and recheck the overflow; if the roller position is too close to the feed end, reposition the roller; if the flow is surging, install the flow surging controller or improve the feed state before the magnetic separator is fed; if the bottom of the roller is blocked, install the flow surging controller at the roller Place a rubber belt at the bottom to check (move from one side to the other). If any blockage is found, lift the roller to remove the blockage.
Fault 3: low specific gravity of concentrate
Treatment: if the magnet position is too high, replace the magnet position; if the water level is too high, readjust the size of tailing bushing; if the discharge gap is too wide, move the drum forward.
Fault 4: uneven distribution of magnetite powder at discharge
Treatment: if the roller is not parallel to the discharge gap, adjust the roller position; if the water tank and roller are not parallel, adjust them with gasket until they are level; if the bottom of the roller is blocked, check and remove the blockage.
Fault 5: worn roller skin
Treatment: there are foreign matters between scraper and rolling skin, check and clean them.
Fault 6: high level in buffer tank
Treatment: if there is fiber or carbon block in the grid, clear the fiber and sundries in the grid in time.
Fault 7: tailing pipe blocked
Treatment: there are many foam gangues. Check and wash the foam gangue under the roller frequently.
Fault 8: concentrate pipe blocked
Treatment: lack of water, increase water supply.
Fault 9: block coal at the feed inlet is blocked
Treatment: if the sieve plate in the dilute medium section of the demineralization screen is rotten or broken, replace the sieve plate in time; if the medium adding pump enters the lump coal, add the medium pump and the mesh grate; if the sieve plate in the combined medium section is rotten, replace the sieve plate.
Common Faults of Centrifuge and Their Solutions
Fault 1: motor fails to start or stops in operation
Phenomenon: the motor cannot be started or stopped in operation after power transmission
Treatment: check the oil level and pressure switch, supplement oil or repair and replace the pressure switch.
Fault 2: motor current high
Phenomenon: motor overcurrent trip
Treatment: check whether there is excessive feeding, check whether the product fines accumulated in the base block the base, check whether there is material stuck between the scraper, whether the bearing or gear is damaged, and make corresponding treatment.
Fault 3: too many solid particles in the filtrate
Phenomenon: there are too many solid particles in the filtrate
Treatment: check whether the screen basket is worn and leaking, and replace it.
Fault 4: low oil pressure on the pressure side of the pump
Phenomenon: low oil pressure of pressure gauge
Treatment: the filter is dirty, check and clean or replace it; the oil delivery pipeline (suction or pressure pipeline) is damaged or blocked; the oil level is low and make up oil.
Fault 5: amplitude reduction
Phenomenon: other normal, vibration reduced
Treatment: aging of rubber spring, changing gasket, increasing vibration times or replacing new rubber spring.
Fault 6: additional noise
Phenomenon: additional noise
Treatment method: loose screws of some parts and fasten them after shutdown.
Fault 7: high product moisture
Phenomenon: high moisture
Treatment: the screen seam is blocked by slime; the feeding amount is large and the water content is high; the particle size is too fine; the screen basket is flushed correspondingly to reduce the feeding and adjust the amplitude.
Fault 8: large swing of screen basket or shell during idling
Phenomenon: large swing when idling
Treatment: the screen basket is unbalanced; the screen basket is not concentric with the main shaft; the screen basket swings with respect to the main shaft; the materials in the screen basket are piled up; the corresponding dynamic balance check and counterweight are carried out, the screen basket is reinstalled, the bolts are tightened, and the materials in the screen basket are removed.
Fault 9: large swing of screen basket and shell after feeding
Phenomenon: large swing in operation
Treatment: the feeding point is too high and the feeding is interrupted; the feeding is mixed with sundries such as iron, which causes the rotor to lose balance; the screen is stuck and damaged; the rotor is out of balance; the feeding moisture is high and the viscosity is large, which is easy to form a group; the axial clearance of the bearing near the end of the large belt pulley is large; the bearing near the end of the screen basket is excessively worn and the radial clearance is large; corresponding treatment shall be carried out.
Common Pump Faults and Solutions
Fault 1: the pump is not loaded or the displacement is insufficient
Phenomenon: the pump is not loaded and the displacement is insufficient
Treatment: check whether the water absorption height exceeds the allowable value, check whether the triangle belt is loose, check whether the material is thick, check the sealing condition of the suction pipe or the filler, prevent air leakage, check whether the suction pipe is blocked, and clean up; check the pump's steering direction, check whether the impeller is damaged; check whether the feed valve is open, and whether the discharge pipe is blocked; the clearance between the impeller and the guard board is too large, And do the corresponding treatment.
Fault 2: Bearing Overheating
Phenomenon: the bearing component is heated, exceeding the normal temperature
Treatment: check the quantity and quality of bearing grease, check whether the bearing is damaged and make corresponding treatment.
Fault 3: short bearing life
Phenomenon: the service life of replaced bearing components is short
Treatment: check the alignment or parallelism of motor shaft and pump shaft, check the bending degree of shaft, foreign matters or improper amount of lubricating grease entering the bearing, check whether there is friction in the pump or impeller is out of balance, and make corresponding treatment.
Fault 4: serious leakage at packing
Phenomenon: serious leakage at the packing
Treatment: check whether the packing and shaft sleeve are seriously worn, check whether the sealing water is clean and deal with it.
Fault 5: pump vibration, high noise
Phenomenon: abnormal vibration and loud sound of pump
Treatment: suction pipe intake, blockage, clear the intake, clear the blockage, check the impeller wear, check whether it is unbalanced, if it is unbalanced, replace the impeller; the flow is uneven, the pump is evacuated, and improve the feeding condition of the pump.
Fault 6: excessive shaft power
Phenomenon: excessive starting load
Treatment: the packing gland is too tight, the packing is hot; the belt of the driving device is too tight; the motor shaft is not aligned or parallel to the pump shaft, the impeller balance plate is not installed correctly, and the rotating part and the fixed part have friction or collision, which should be solved accordingly.
Any need just feel free to contact us:
Lynette Jing
Email: lynette@miningmes.com
Tel/WA:+86 19113498960