
Company:China Mineral Processing & Metallurgy League
Email: sales@hot-mining.com
Phone:+86 18252116933
Fax:+86 10 58646590
Address:Room10811, Floor8, Building A, Galaxy SOHO, Dongcheng Dist, Beijing, P.R.China
Fully mechanized coal mining method for low coal seam under complicated geological conditions
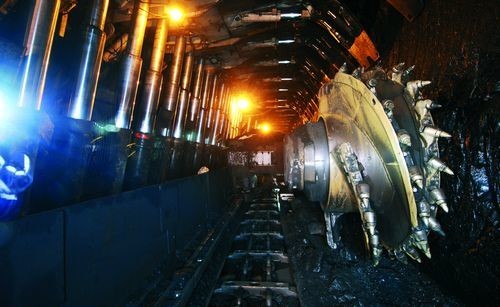
The schematic diagram of three-machine system
In order for the three-machine system to achieve a productivity above 300~400 t/h when the thickness of coal seam is 0.6~0.8 m, and the system still works appropriately when the thickness is 0.9 m, a number of technical measures were taken, including high strength supports, low profile frames, top-beam electro-hydraulic control, low profile shearer that ensured lower limit height to machine passing, high strength scraper conveyer with low trough and others. The schematic diagram of threemachine system is shown in Figure 1, in which the shearer model is LWS160/360-WD. The hydraulic powered support model is ZY3300/07/13 and the conveyer model is SGZ630/220.
Parameters of the three-machine system
The reduction of the scraper conveyer middle trough height was the key when reconstructing the three-machine system to lower its profile. Therefore, technological innovation was applied in the following several aspects: reducing the height of middle trough; reducing the unloading height of scrapper; reducing the diameter of scrapper coupling connecting shields; making the machine head and end exchangeable; using imported decelerators; employing the two-speed starting mode; and making transport capacity adapt to high production rate. The technological innovation enabled the entire machine system to have high strength and reliable performance. After the revision and based on the strength calculation, the height of middle trough was reduced to 208 mm and the minimum coal crossing height was 226 mm, achieving the lowest extreme dimension. The height of machine head and end was reduced to 720 mm, realizing an unloading height of 460 mm. The width between the center of chain wheel of machine head and end, and the center of decelerator was 910 mm, meeting the requirements.
The top-beams of hydraulic powered supports were designed to have an overall rigid structure, reducing the thickness of top-beam front end, allowing sufficient height for the machine crossing when the extraction height is 0.9m. The shearer was designed into one integrated structure. To farthest reduce the height and length of machine fuselage, the non-machine-carry variable frequency electric drive was utilized. The scrapper was designed to be short-trough-side and ride-apron type for adapting to thin coal seam with working face fluctuations, and to ensure meeting the requirements of three-machine mating height. The essential sizes of the three-machine system mating equipment are shown in Table 1:
The first realization of cutting the top-and-bottom rocks with hardness f5 at the coal thickness less than 0.9 m–highly improved rock breaking capability
When the shearer cuts the top-and-bottom rocks in extremely thin coal seams, it will cause vibrations and impacts. It requires high power (especially the cutting power), greater weight, and high degree of integrity and stability of the mechanical drive and cutting systems. This study applied highly efficient and strong mechanical drive and cutting systems to improve the rock breaking capacity. The improved system can cut the top-and-bottom rocks with hardness coefficient f5 at coal seam thickness below 0.9m.
The first application of ultra-high-temperature laser cladding technology to achieve sparkless cutting
The designed and applied highly effective force wear-resisting sparkless pickaxe-tooth roller is shown in Figure 2. When breaking bottom rocks, the shearer takes the force wear-resisting sparkless pickaxe-tooth to avoid producing the spark in the process of rock cutting. This technology meets the GB13813 standard testing requirements.
The first application of the lead angle friction theory and the vertical-andpushing movements of the sloping panel principle to develop moldboard coalloading equipment
For the roller type thin coal seam shearer, since the shallow drum spiral groove resulted low coal-loading efficiency, the shearer’s coal-loading needed improvement and, therefore, the multi-way coal-loading was used.
According to the shearer working pattern and the coal falling characteristics, in addition to loading coal by the roller, coal which falls in front of the scraper conveyer is loaded by the moldboard coal-loading equipment, which resembles the farming plow and the plow board is made with high strength and wear-resistant materials and is installed separately underneath the rocker arms. It loads the coal to the scraper conveyer during the operation. The experiment shows that it achieved a coal-loading efficiency of above 90%.
The first application of electro-hydraulic control technology and remote control of a shearer, and realizing main work stage automation, and rapid movement of the shearer-support system
Hydraulic powered supports were equipped with six-function PM32 electro-hydraulic control system. The system applied modern new technologies such as the electromagnetism first pilot valve, advanced and reliable pressure and displacement sensors, nimble and flexible programming microprocessor as well as multi-cores and position processing. It greatly speeded up the support’s movement, secured the rated initial holding load of the supports, achieved movement of supports under pressure, achieved support movement in groups, achieved multiple ways of control, and also achieved successful monitoring and control of support pressure and position.
The application of electro-hydraulic control system and the remote control technology to the extremely thin coal seam enabled the main work stage programmable control at coal mining working face. This programmable control technology has been applied in the hydraulic powered supports with the 2200 L/min emulsion pumping station and the PM32 hydraulic powered supports electro-hydraulic control system. The movement time of each support is as short as 6 seconds and machine following speed is 6 m/min. These improvements of the main work stage automation dramatically increased the longwall working surface output and significantly enhanced the work efficiency.
The first application of optimized structure design with advanced computer simulations for stress and performance parameter analysis for the hydraulic powered supports
The overall design of the hydraulic powered supports is top-beam and two-column shield type, with non-side guard shield. The design has a simple structure, low center of gravity, high stability, strong torsion loading capacity, and simple and direct movement action. Equipped with high capacity pumping station, the hydraulic supports can be mobilized quickly. The design of the hydraulic powered supports was based on the parametrization and visualized dynamic simulations including the finite element simulations. The experimental results are as shown in Table 2.
The support model ZY3300/07/13 thin coal seam two column shield type was selected based on the above simulation and analysis.
CONCLUSIONS:
(1) The first application of electro-hydraulic control technology and remote control of a shearer, and realizing main work stage automation, and rapid movement of the shearer-support system.
(2) The technology developed the highly effective force wear-resisting sparkless pickaxe-tooth which cuts the coal crag 68295 tons without truncation-tooth damage and without sparks during the industrial experiment and hads very strong applicability to the mining of thin coal seam.
(3) After analysis of the coal-loading condition, we take the roller and moldboard coal-loading equipments which adapt to the mining of extremely thin coal seam and further enhance the coal-loading effect. 176 Fully mechanized coal mining technology for thin coal seam under complicated geological conditions
(4) It realizes the automation of thin coal seam fully mechanized coal mining. Since no worker is required at the operating workstage with remote control, the mine production safety is enhanced and productivity is significantly increased.
If you are interested, pls contact us:
Email: kira.zhang@hot-mining.com
Tel/WA:+86 15281051932
Email: luke.jiao@hot-mining.com
Tel/WA:+86 183 2857 9853